All running clearances, fitting tolerances and dimensions are given in 'Technical Data'.
E.1. - GENERAL DESCRIPTION - Section Menu
The engine is a four cylinder four stroke, twin overhead camshaft unit having a cast aluminium cylinder head, which has fully machined hemispherical combustion chambers and separate ports for each valve. The valves, of which the inlets are longer than the exhaust, have replaceable guides and seat-inserts and are at an angle of 27° to the vertical. They are operated by the camshafts acting directly on piston type cam followers (tappets). A spring tensioned single row chain drives the camshafts at half engine speed. The camshaft end float and location depends on a shoulder at the front of each shaft bearing in the head. The timing chain also drives the jackshaft which is situated in the right-hand wall of the cast-iron cylinder block and which drives the oil pump, distributor and fuel pump. The jackshaft is located by a thrust plate bolted to the cylinder block front face and runs in three steel-backed white metal bearings, while the camshafts each run in five bearings of this type. The oil pump, distributor and fuel pump are mounted on the right hand side of the engine, the oil pump and distributor being driven by a single skew gear on the jackshaft and the fuel pump by a cam also on the same shaft.
The crankshaft, of cast iron construction and dynamically balanced, runs in five steel-backed lead bronze lined bearings, end float being controlled by split thrust washers located in the cylinder block on either side of the centre main bearing.
The connecting rods of 'H' section forgings have steel-backed bronze little end bushes and steel-backed copper lead big end liners, the big end bearing caps being located by two dowels and retained by two bolts. Solid skirt aluminium alloy pistons with two compression and one oil control ring situated above the gudgeon pin are used. The gudgeon pins are retained in position by circlips installed in grooves at each end of the gudgeon pin bore.
A cast-iron flywheel incorporating a steel ring gear drive for the starter, is located on the crankshaft flange and retained by six bolts fitted without lockwashers.
E .2. – LUBRICATION - Section Menu
General
The lubrication system is of the forced feed type, the oil being circulated by a mechanically driven oil pump bolted to the right-hand side of the cylinder block. The pump is driven by a skew gear on the jackshaft, and is of the eccentric bi-rotor type which incorporates a non-adjustable plunger type relief valve.
Oil is drawn from the sump up an inlet pipe attached to the cylinder block and into the pump. When the relief valve opens, oil is passed back into the sump, returning via the base of the sump to prevent aeration. From the pump the pressurized oil flows through the integral full flow filter to a short oil gallery on the right-hand side of the engine. At the forward end of the gallery is a tapped take-off for the oil pressure transmitter. A cross drilling at the rear of the gallery takes the oil to the other side of the engine where the main oil gallery is situated from which all the main bearings are fed. A notch cut in the centre main bearing liner feeds oil to the crankshaft rear thrust washer. Oil is fed to the big end bearings through drillings in the camshaft front, centre and rear journals. Lubrication of the little end bushes, the gudgeon pins and the non thrust sides of the cylinders is by oil mist and an oil jet forced through a small drilling in each connecting rod web at every revolution of the crankshaft.
The jackshaft bearings are fed from the front, centre and rear main bearing via drillings in the block and a metered jet of oil from a front drilling lubricates the chain and sprockets. Oil fed to the overhead camshafts is controlled by flats machined on the jackshaft front journal, and each camshaft bearing is then fed by a central drilling, blocked at the rear end by a tapered Allen screw. Surplus oil from these bearings is then drained back into the sump by way of passages in the head.
Oil Level
- More Info -
The correct level is to the 'FULL' mark on the dipstick, which is located to the left-hand side of the timing cover. When checking the oil level the car must be standing on a level surface and the dipstick withdrawn, wiped, replaced and finally withdrawn and read, the depth of the oil on the end of the dipstick indicating the level of the oil in the sump. If oil needs to be added, remove the oil filler cap on the camshafts cover and pour in clean engine oil of the correct grade, (see Section 'O') until the dipstick indicates that the sump is full. Do NOT overfill. Replace the oil filler cap securely (double notch) otherwise an oil loss could occur, with the resultant failure of the entire engine lubrication system. From new the oil should be changed after 500 miles (800 kin.) and then every 5,000 miles (8,000 kin). If the oil appears to be excessively dirty before this distance, it should be changed and a new filter element fitted.
The sump capacity is given in 'Technical Data'. Where possible, it is better to drain the oil when the engine is warm (after having just completed a run) and has a lower viscosity to carry away any sediment.
Oil Filter
A full-flow throw away canister type filter is screwed on to an adaptor in the oil pump to make an integral unit, the oil flowing through the filter to the oil gallery. To remove the filter, turn in an anti-clockwise direction. Fully unscrew and discard, together with its sealing ring. The filter should be replaced at intervals of every 5,000 miles (8,000 km.), or more frequently if there are any signs of excessive fouling.
Section 'O' (Lubrication & Maintenance) contains fuller information on renewing the oil filter.
Oil Sump
E.3. ENGINE TUNE - Section Menu
- Pull off the sparking plug leads and remove the plugs. Clean the plugs and reset the gaps to the dimensions given in 'Technical Data', or if the electrodes are badly burned, fit new plugs, and reconnect the plug leads.
- Remove the distributor cap and examine the contact breaker points. Replace the points if badly burned or excessive metal transfer is evident. Adjust the points gap to the dimensions given in 'Technical Data' and refit the distributor cap.
- Remove the fuel pump sediment bowl and filter screen. Wash both in clean petrol, ensure that the gasket is in good condition and refit screen and sediment bowl to the fuel pump.
- Remove the air cleaner element and clean by shaking through. If very clogged with dust or dirt, replace. Clean filter body of all accumulated dirt, reassemble and refit air cleaner assembly to car.
- Disconnect the fuel feed pipes at the carburetters.
- Dellorto Carburetters - Remove jet covers with its gasket by releasing the securing screws. Unscrew the main jets and the slow running jets. Blow them clear with an air line. Do NOT use wire, as this will enlarge the jet orifice. Replace the jets, gasket and cover. Remove the screwed plug to gain access to the pump jets. Repeat cleaning process as for the main and slow running jets.
- Zenith Stromberg Carburetters - Disconnect air trunk from air box and remove air box. Remove carburetters from engine (see Section 'L') to a clean workbench. Release centre plug from the base of each carburetter. Remove float chambers by releasing the retaining screws, and withdrawing in a vertical motion to avoid damage to the float mechanism. Remove float chamber gasket. Take out floats. Remove needle valve from float chamber cover. Remove 'O' ring from centre plug. Thoroughly clean all removed parts in clean petrol. Refit needle valve into float chamber cover using a new washer. Replace float assembly and check (see Section 'L'). Refit float chambers with new gasket. Fit new 'O' ring to centre plug and replace securely. Refit carburetters to engine using new gaskets. Top up damper reservoirs with oil (see Section 'O').
- Reconnect the fuel feed pipes at the carburetters.
- Adjust the valve clearances. (Section 'E7')
- Connect the leads of a timing light in accordance with the manufacturers instructions. Check that the mark on the crankshaft pulley is visible; if not, mark with paint.
- Start the engine and point the timing light at the crankshaft pulley, adjacent to the timing scale. Progressively increase the engine speed to 2,500 r.p.m, observing the timing mark, with the aid of the timing light to check that the distributor advances the ignition timing.
- At 2,500 rev./min, adjust the ignition timing if necessary (see 'Technical Data') by slackening the distributor clamp and turning the distributor body as required. After making an adjustment tighten the clamp only sufficiently to hold the distributor in position - DO NOT OVERTIGHTEN. Remove the timing light.
- Adjust the slow-running speed of the engine (see Section 'L').
E.4. - COMPRESSION CHECK - Section Menu
- Warm up the engine to its normal operating temperature then remove all sparking plugs. Set throttles to fully open position.
- Place the gauge in a convenient position and insert the conical-ended rubber tube into No. 1 sparking plug orifice. The normal compression pressure with an engine that has been run in correctly is given in 'Technical Data'. At altitudes above sea-level, proportionally lower pressures will be obtained. Compression is checked with starter turning engine at 200 r.p.m. Battery and starter should be in good condition.
- Test the remaining cylinders in a similar manner, replace sparking plugs and connect the plug leads.
E.5. - CAMSHAFT COVER - Section Menu
To remove.
- Remove the eight nuts and washers retaining the camshafts cover.
- Remove the cover together with its gasket.
To Replace.
When refitting the camshafts cover, it is advisable to use a new gasket to which jointing compound (Part No. A036E6027) has been applied.
E.6.- TIMING CHAIN TENSIONER - Section Menu
- The timing chain tensioner is located at the right-hand side of the engine immediately below the cylinder head flange. Release the locknut and screw in (or out) the tensioner until a minimum noise level is achieved, approximately .5 in. (12.5 mm.) total movement of the chain between the two camshaft sprockets.
E.7. - VALVE CLEARANCES - Section Menu
To Remove
- Remove the camshafts cover (Section 'E .5').
- Turn the camshaft until the heel of the cam is on the cam follower (tappet) then using feeler gauges, determine the distance between the cam follower and the cam heel. This clearance is given in 'Technical Data'.
- Check all valve clearances, noting any which require adjustment.
- Remove the camshaft.
- Remove the cam followers with the aid of a valve grinding tool, keeping them in their respective order.
- Remove each adjustment shim now exposed, where the clearance requires adjustment, and substitute shims (one only to each valve) giving the correct clearance. A thinner shim will be required to increase the valve clearance, and a thicker one to reduce the clearance.
Select a shim to give the correct size from the following Formula:
Shim thickness required = A.C. + E.S. - CC.
Where
A.C. is actual valve clearance
E.S. is existing shim thickness
C.C. is correct valve clearance.
Measure the thickness of the shim accurately with a micrometer, even though the shims thickness is etched around the periphery or on the underside of the shim.
Any roughness caused by the etching should be removed with fine emery cloth.
To Replace
- Refit the cam followers in their respective bores.
- Fit the camshafts and recheck the valve clearances, re-adjusting if necessary.
- Refit the camshafts cover.
E.8. CAMSHAFTS SPROCKETS AND TIMING CHAIN - Section Menu
To Remove
- Remove the camshafts cover (Section 'E.5.).
- Set the engine in the timing position by aligning the timing mark on the flywheel with the mark on the clutch bellhousing. At this point the timing marks on the camshafts sprockets should be adjacent to each other and level with the camshafts cover mounting Face.
- Remove the timing chain tensioner (Section 'E.6.').
- Remove the sprockets by releasing their central retaining bolts, and disconnect the timing chain. To remove the timing chain the front cover (Section 'E.30.') must first be removed.
To Replace
- Fit the camshafts sprockets and timing chain aligning the timing marks, as set during dismantling.
Tighten the retaining bolts to the torque loading given in 'Technical Data'.
Ensure the correct sprocket replacement (Ex. sprocket on exhaust camshaft).
- Refit and adjust the timing chain tension (Section 'E.6.').
- Check ignition timing.
- Refit the camshafts cover (Section 'E.5.').
E.9. - CAMSHAFTS AND BEARINGS - Section Menu
To Remove
- Remove the camshafts covers. (Section 'E.5.').
- Set the engine in the timing position.
- Remove the timing chain tensioner.
- Remove the camshafts sprockets.
- Remove the alternator driving belt (See Section 'M').
- Remove the bolts securing the camshafts bearing caps, and remove the caps marking them (if not already marked) to ensure replacement in their original position.
- Extract the bearing liners.
To Replace
- Fit new bearing liners, noting that the location tags are correctly positioned in their locations in both cylinder head and bearing caps.
- Fit the camshafts and their bearing caps, tightening the cap bolts progressively from the centre working outwards, to the torque loadings given in 'Technical Data".
- NOTE: The oil seal on the inlet shaft is fitted with the aid of a Lotus Special Tool 'PT. 0020', as shown in illustration.
- Fit the camshafts sprockets and adjust the timing chain tension.
Check and adjust the valve clearances.
Finally, fit the camshafts cover, followed by the alternator driving belt.
E.10. - CYLINDER HEAD - Section Menu
To Remove
- Drain the cooling system.
- Remove the carburetters air box (see Section 'L').
- Remove radiator top hose and the heater hose from their connections at the cylinder head.
- Disconnect the water temperature gauge sender unit.
- Disconnect the throttles and choke cables, fuel pipes from carburetters and exhaust manifold.
- Remove camshafts covers.
- Remove the camshafts sprockets.
- Remove the alternator driving belt.
- Pull the leads from the sparking plugs.
- Release the cylinder head bolts evenly and progressively working diagonally from the centre, not forgetting the bolts in the timing cover, and remove the cylinder head together with its gasket. Do NOT lay the cylinder head flat on its face while the camshafts are fitted as this will cause damage to the valves.
To Replace
- Screw into diagonally opposite holes (front left, rear right) in the cylinder block face, two spare cylinder head bolts from which the heads have been removed and screwdriver slots cut.
- These studs locate the gasket whilst the cylinder head is being fitted.
- Use a new cylinder head gasket and a new cork gasket on top of the front cover.
- This cork gasket should have jointing compound (Part No. A036E 6027) applied to its face, which will be in contact with the cylinder head.
- Fit the cylinder head assembly, ensuring that the breather pipe is engaged in its bore.
- Loosely replace the cylinder head bolts.
- Extract the two gaskets locating studs and fit the last two bolts.
- Tighten all bolts to the torque loading given in 'Technical Data' working progressively diagonally outwards from the centre.
- New cylinder head bolts (Part No. 26E 027A) have recently been introduced, these having an improved material specification.
- There is no change to the tightening torque.
- Old and new bolts are interchangeable, but it is inadvisable to mix old and new bolts on the same cylinder head, as the thread lengths may differ slightly.
- Fit the camshafts sprockets, alternator driving belt and camshaft cover.
- Reconnect the exhaust manifold, throttle and choke cables, and fuel pipes to carburetters. Refit the brake servo vacuum hose, radiator top hose, water temperature gauge sender unit and the heater hose. Refit the carburetters air box.
- Finally, refill the cooling system.
E.11. - VALVES - Section Menu
To Remove
- Remove the cylinder head and the camshaft.
- Remove the cam followers and the adjusting shims.
- Using a valve spring compressor, compress the valve springs and extract the split collets, valve spring retainer, valve springs and spring seat from each valve.
- Remove the valve.
To Replace
- Lightly lubricate the stem of the valve and insert into its guide.
- Fit spring seat, valve springs, valve spring retainer.
- Place the valve spring compressor in position and compress the valve springs sufficiently to fit the split collets.
- Remove the valve spring compressor.
- Replace the cylinder head followed by the camshafts.
- Fit file camshafts sprockets, check the valve clearances and finally fit the camshafts cover.
E.12. - DECARBONIZE CYLINDER HEAD AND PISTONS - Section Menu
- Remove carburetters.
- Remove cylinder head.
- Remove the valves.
- Using a suitable implement such as a blunt scraper, remove all carbon deposits from cylinder head faces, inlet and exhaust ports, piston crowns and valve heads.
A ring of carbon should be left around the periphery of each piston crown.
The top of the cylinder bores should NOT be touched.
- Clean each valve thoroughly and carefully examine for pitting.
Valves in a pitted condition should be refaced with a suitable grinder or new valves should be fitted.
Stamp any new valve with the number of the port to which it is fitted.
If the valve seats show any signs of pitting or of unevenness they should be trued by the use of service cutting tools.
When using a cutting tool take care to remove only as much metal as is necessary to ensure a true surface.
The removal of too much metal could cause the spring retainer to foul the cam follower and/or cause difficulty in achieving the required valve clearances.
- When grinding a valve onto its seating the valve should be smeared lightly with fine or medium Carborundum paste and then lapped in with a suction grinder.
Avoid the use of excessive quantities of grinding paste and see that it remains in the region of the valve seating only.
A light coil spring placed under the valve head will assist considerably on the process of grinding.
The valve should be ground to its seat with a semi-rotary motion and occasionally allowed to rise by the pressure of the light coil spring.
This assists in spreading the paste evenly over the valve face and seat.
It is necessary to carry out the grinding operation until a dull, even matt surface free from blemishes is produced on the valve seat and valve face.
On completion, the valve seats and ports should be cleaned with a rag soaked in paraffin, dried, and then thoroughly cleaned by compression air.
The valves should be washed in paraffin and all traces of grinding paste removed.
Check that no grinding paste has entered the valve guides.
- Re-assemble the valves to the cylinder head.
- Refit cylinder head and carburetters.
E.13. - VALVE SEAT INSERTS - Section Menu
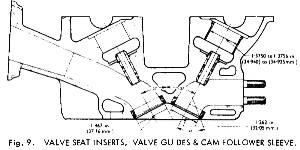
To Remove
- Remove the cylinder head and dismantle as for decarbonising.
- Remove the valve seat inserts by milling through, or almost through (dependant on the skill of the operator), the edge of the insert, whereupon the seat should collapse.
In the case of a stubborn seat, it is permissible after milling, to start the seat on its way to removal by inserting a suitable drift through the appropriate port and gently tapping the seat from its recess.
Ensure that the recess in the cylinder head is ENTIRELY FREE OF FOREIGN MATTER, otherwise the new insert will NOT seat fully in the recess.
To Replace
- Valve seat inserts are available in standard and up to .015 in. (.38 mm.) oversize.
- Heat the whole cylinder head to a temperature NOT EXCEEDING 200°C. (392°F) and freeze the insert with dry ice to a temperature NOT LESS THAN -80°C. (-112°F).
- Press the insert into place using a suitable replacer tool ensuring that the seat faces towards the combustion chamber.
Allow the cylinder head to cool naturally in the air.
- Rebuild and refit the cylinder head.
E.14. - VALVE GUIDES - Section Menu
To Remove
- Remove the cylinder head and dismantle.
- Remove the valve guide with a suitable drift, knocking upwards into the cam follower bore after heating the cylinder head to 100/150°C. (212/303°F.).
To Replace
Valve guides are available in standard and up to .006 in. (.152 mm.) oversize.
- Heat the cylinder head to 100°/150°C (212/303°F.), locate new circlip on the new guide and press the guide into its bore until the circlip seats completely in its recess.
Care must be taken that the guides are NOT driven beyond this point (See 'Technical Data').
- Ream the guide AFTER fitting, to the dimensions given in 'Technical Data'. Re-cut the valve seat to ensure that it is concentric with the valve stem bore.
- Rebuild and refit the cylinder head.
E.15. - CAM FOLLOWER SLEEVES - Section Menu
To Remove
- Remove the cylinder head (Section 'E.10') and dismantle (Section 'E.12').
- Remove the cam follower sleeve by cutting a groove adjacent to each scallop, taking care that the cylinder head is NOT damaged.
- Using a suitable sharp chisel remove the sleeve from its location, again taking care NOT to damage the cylinder head.
To Replace
- Heat the whole cylinder head to 150°C. (302° F).
- Press the sleeve into place using a suitable tool and machine after fitting to the dimensions given in 'Technical Data'.
Re-cut the scallops.
- Rebuild and refit the cylinder head.
E.16. - OIL SUMP - Section Menu
To Remove
- Using a suitable receptacle, release the drain plug and allow the oil to drain.
- Remove the starter motor, bell housing lower cover, oil filter and the exhaust downpipe together with the silencer.
- Release the setscrews from around the periphery of the sump and remove sump.
To Replace
- When replacing, which is a reversal of the removal procedure, use jointing compound (Part No. A036 E 6027) on the sump gaskets before bringing into contact with the cylinder block.
E.17. - MAIN BEARINGS [1] - Section Menu
To Remove
- Remove the oil sump (Section 'E.16').
- Mark each cylinder bearing cap (if not already marked) with a similar mark on the cylinder block adjacent to the crankshaft, so that each cap when refitted will be in its original position.
- Remove No. 1 (from front end) main bearing cap, and release the upper shell bearing from the cylinder block by pushing out, revolving the crankshaft at the same time.
Release the lower shell bearing from the cap by lifting out.
To Replace
- Fit new bearings by reversing the dismantling procedure and refit No.1 bearing cap.
- Tighten the retaining bolts to the torque loading given in 'Technical Data'.
- Renew remaining main bearing liners in sequence, tightening each bearing cap to its correct torque loading BEFORE releasing the next one in sequence.
E.18. - CONNECTING ROD BEARINGS [2] - Section Menu
To Remove
- Remove the oil sump (Section 'E.16').
- Commencing with No.1 (from front end) connecting rod, turn the crankshaft to facilitate removal of cap and mark cap and rod.
- Release the big-end bolts by two or three turns, and tap them to release the cap.
Fully unscrew the bolts and remove the cap.
- Remove the upper and lower big-end bearing liner from the connecting rod and the lower bearing liner from the connecting rod cap.
To Replace
- Replace the lower and upper big-end bearing liners in their appropriate locations,
- Fit the cap to the connecting rod and tighten the bolts to the torque loading given in 'Technical Data'.
- Renew the big-end bearing liners by repeating the above operation.
E.19. -PISTONS, PISTON RINGS AND CONNECTING RODS - Section Menu
To Remove
- Remove the cylinder head (Section 'E.10') and the oil sump (Section 'E.16').
- Release the big-end bolts by two or three turns, and then tap them to release the cap.
Fully unscrew the bolts and remove the cap.
Push the piston out of the bore and remove the assembly to a bench.
- Remove the piston rings.
Extract the gudgeon pin circlips and push the pin out of the piston.
Separate the piston and the connecting rod.
To Replace
- Select the new piston of the appropriate grade required (see 'Technical Data').
- Fit the piston rings, oil control first, followed by the lower then the upper compression rings.
Ensure that the rings are fitted the correct way up.
E.20. - CRANKSHAFT PULLEY - Section Menu
To Remove
- From beneath the car, release the central retaining bolt and using a suitable puller, remove the pulley together with the water pump driving belt.
To Replace
- Reverse the removal procedure.
NOTE: There is NO adjustment to the belt.
E.21. - WATER PUMP PULLEY AND BELT - Section Menu
To Remove
- From beneath the car, release the bolts ('B' of Fig. 12) securing the water pump pulley to its mounting flange.
- Pull off the pulley, together with the water pump driving belt.
To Replace
- Reverse the removal procedure
NOTE: The above procedure applies when either the belt, the pulley, or both parts require removal.
There is NO adjustment to the belt.
E.22. - OIL PUMP AND OIL FILTER - Section Menu
- Release the three securing setscrews and remove the pump and filter as an assembly.
To Dismantle
(All clearances are given in 'Technical Data')
- Remove the filter element by unscrewing in an anti-clockwise direction.
- Remove the end plate and withdraw the 'O' ring from the groove in the pump body.
- Check the clearance between the lobes of the inner and outer rotors. The rotors are supplied as a matched pair only, so that if clearance is excessive a new rotor pair must be fitted.
- Check the clearance between the outer rotor and the housing. If clearance between the outer rotor and pump body is excessive a new rotor assembly and/or pump body should be fitted.
- Place a straight edge across the face of the pump body and check the clearance between the face of the rotors and the straight edge. If this clearance is excessive the face of the pump body can be carefully lapped on a flat surface.
- If it is necessary to renew the rotor or drive shaft, remove the outer rotor, then drive out the remaining pin securing the skew gear to the drive shaft and pull off the gear. Withdraw the inner rotor and drive shaft.
To Reassemble
- If the pump has been carefully dismantled, fit the inner rotor and drive shaft assembly to the pump body.
Press the skew gear (if undamaged) onto the drive shaft end supporting the shaft, at the rotor end, on a suitable spacer.
Replace the gear retaining pin and peen over the ends securely.
- Install the outer rotor with its chamfered face inwards, towards the pump body.
Check clearance where shown by arrows.
- Place the '0' ring in the groove in the pump body and fit the end plate with the machined face towards the rotors.
- Fit a new filter element, after ensuring that both the mating face on the oil pump body and the oil filter element are clean, then apply a film of engine oil to the rubber seal which is in contact with the oil pump body.
Screw on the filter by HAND just sufficient to make a seal, usually 2/3 to 3/4 turn to ensure an oil tight joint.
To Replace
- Place a new gasket on the pump mounting flange and fit pump and filter as an assembly.
- Tighten the securing bolts to the torque loading given in 'Technical Data'.
E.23. - FRONT (TIMING) COVER OIL SEAL - Section Menu
To Remove
- Remove the crankshaft pulley (Section 'E.20').
- With a suitable extractor, remove the oil seal, taking care NOT to damage the casing when removing.
To Replace
- Using a hollow drift, the outer diameter of which is the same size as the oil seal insert a new seal.
- Replace the crankshaft pulley.
E.24. - TIMING CHAIN TENSIONER SPROCKET - Section Menu
To Remove
- Remove the camshafts cover (Section 'E.5').
- Set the engine to T.D.C. (Section 'E.8').
- Remove the timing chain tensioner by fully unscrewing.
- Remove the INLET camshaft sprocket (Section 'E.8').
- Using a suitable piece of wire with a hooked end, insert the hook into the sprocket then release the pivot pin.
Remove bracket and sprocket assembly by passing up between the two camshafts.
- Unscrew the sprocket pin and remove sprocket.
To Replace
- Reverse the removal procedure, not forgetting to tighten the bolts, where necessary, to the torque loadings given in 'Technical Data'.
E.25. - FLYWHEEL AND RING GEAR - Section Menu
To Remove
- Remove the transmission (see Section 'F' of the main Europa manual).
- Remove the chassis cross members as follows:
- Release the bolts securing the upper end of the rear dampers to the horizontal member.
- Release the bolts securing the diagonal braces to the chassis and the bolt securing the forward end of the braces to the horizontal cross member.
- Remove the chassis cross members.
- Unscrew the bolts around the periphery of the clutch assembly and remove clutch from flywheel.
- Release the six bolts and remove the flywheel.
- Cut between the two adjacent teeth on the ring gear with a hacksaw and split the gear with a chisel.
NOTE: Under no circumstances must pressure be applied in an attempt to remove the gear for re-positioning on the flywheel.
To Replace
- Heat the new ring gear evenly, to a temperature NOT EXCEEDING 600°F. (316°C.).
Do NOT heat beyond this point otherwise the wear resistance properties of the gear will be destroyed.
Fit the gear to the Flywheel with the chamfers on the leading faces of the teeth relative to the normal direction of rotation.
Allow the ring gear to cool naturally in the air. DO NOT QUENCH.
- Locate the flywheel squarely upon the crankshaft flange insert the securing bolts and tighten to the torque loading given in 'Technical Data'.
- Check the flywheel run-out using a proprietary dial gauge.
The total run-out should NOT EXCEED the dimension given in 'Technical Data'.
- Refit the clutch assembly, centralising the driven plate with a dummy gearbox mainshaft.
Tighten the bolts to the torque loading given in 'Technical Data'.
- Replace transmission and chassis cross members.
E.26. - CRANKSHAFT REAR OIL SEAL - Section Menu
To Remove
- Remove the transmission (Section 'E.25').
- Remove the flywheel (Section 'E.25') and the oil sump (Section 'E.16').
- Extract the retaining bolts and remove the rear oil seal carrier from its location on the cylinder block.
- Using an extractor, remove the oil seal from its carrier.
To Replace
- Fit a new oil seal to the oil seal carrier.
- Locate a new gasket on the rear oil seal carrier using a suitable jointing compound, insert the retaining bolts, and locate carrier squarely on the cylinder block before tightening to the torque loading given in 'Technical Data'.
- Refit the flywheel and the oil sump.
- Refit the transmission.
E.27. - CLUTCH SPIGOT BEARING - Section Menu
E.28. - ENGINE MOUNTING BRACKETS - Section Menu
To Remove
- Chock the front wheels, jack up the rear of the car and support with chassis stands.
- Support the engine with a screw-type jack.
- Remove the right-hand bracket (4 setscrews to cylinder block and 2 bolts with nuts to the mounting on chassis) and replace with a new bracket.
- It is recommended that the setscrews retaining bracket to the engine, be deleted and studs (Part No. A074 E 0490Z), washers (Part No. A05W 1007) and Nyloc nuts (Part No. A074 E 6016Z), used in their place.
Use Loctite 'Studlock' on the thread of the studs into the cylinder block.
Torque load the Nyloc nuts to 2.49 kg.m. (18 lbs.ft.).
- Repeat operations '3' and '4' for the left-hand bracket.
- Remove jack from beneath engine, raise rear of car, remove chassis stands, and lower car to floor.
E.29. - ENGINE ASSEMBLY - Section Menu
To Remove
- Remove the engine compartment lid.
- Disconnect the battery.
- Drain the cooling system by releasing the bottom hose from the radiator.
Remove the hose from the water pump on the front timing cover and the hose from the thermostat housing.
- Drain the transmission casing.
- Disconnect the air trunking from the air cleaner and remove rear luggage carrier.
- Disconnect the following connections from their attachments on the engine:
- Water temperature feed
- Oil pressure pipe
- Alternator feed cables (see Section 'M')
- Exhaust manifold (see Section 'S')
- Heater hoses
- Ignition, distributor and coil cables
- Starter motor cable
- Choke, throttle and clutch cables
- Remove the starter motor. Remove fuel feed pipes from fuel pump.
- Remove the drive shafts (see Section 'D').
- Disconnect the gearshift linkage (see Section 'F'). Disconnect the reverse lamp switch cable.
- Release the bolts securing the upper end of the rear dampers to the chassis crossmember.
Remove the bolts securing the forward ends of the diagonal cross-brace to the chassis and the centre bolt securing the brace to the cross-member and remove the brace.
Release the bolts securing the cross-member to the chassis and remove crossmember.
- Fit a sling and support the engine/transmission unit (power unit) on suitable lifting tackle.
- Remove the engine mounting brackets and lift power unit up and out of engine compartment.
To Replace
Replacement is a reversal of the removal procedure, but the following points should be observed:
- Ensure earthing strap is fitted beneath engine mounting.
- Check the gearshift linkage.
- Re-adjust the clutch cable.
- Bleed the cooling system after refilling.
- Fill the engine sump and the transmission with their recommended oils.
- Reconnect the battery, start engine and check for leaks. Check and re-adjust ignition timing and the carburetters slow running.
- Refit the engine compartment lid.
E.30. - FRONT (TIMING) COVER AND/OR WATER PUMP - Section Menu
To Remove
- Remove the engine assembly (Section 'E.29').
- Remove the cylinder head (Section 'E.10'), water pump pulley and belt (Section 'E.21'), crankshaft pulley (Section 'E.20'), sump (Section 'E.16') and the timing chain tensioner (Section 'E.6').
- Remove the front cover by extracting all the forward facing bolts, of which there are eleven.
- Remove the crankshaft oil slinger by pulling off from the end of the crankshaft.
- Disconnect the timing chain taking care NOT to rotate the camshafts, or the crankshaft, thus altering the timing.
- Remove the jackshaft (auxiliary shaft) sprocket.
- Remove the front cover backplate with its gasket by extracting the single retaining setscrew immediately below the water pump aperture.
- Remove the water pump from the front cover by extracting the pump bearing retaining clip from the slot in the housing.
To Dismantle the Water Pump
- Remove the pump pulley hub from the shaft.
- Press the impeller, seal, slinger, shaft and bearing assembly out of the housing using a suitable press.
Press the impeller off the end of the shaft.
- Remove the pump seal from the shaft.
- Carefully split the slinger bush to detach it from the shaft.
- Remove the insert, with its 'O' rings from the front cover.
To Rebuild the Water Pump
- Using a new shaft and bearing assembly, press into the housing until the groove in the bearing is in line with the slot in the housing.
Fit new clip to retain.
- Press the pump pulley hub on to the front end of the shaft until the end of the shaft is flush with the outer face of the hub.
Fit new slinger bush (flanged end first) on the rear end of the shaft until the flanged end is from 3.17 to 5.08 mm. (.125 to .200 in.) from the end of the bearing.
Fit the new pump seal on the slinger bush with the carbon thrust face towards the impeller.
Press into housing.
- Fit new 'O' rings to insert and fit insert to front cover.
- Press impeller on to the shaft ensuring that the vanes are NOT damaged.
With the impeller correctly fitted there should be between .51 to .76 mm. (.020 to .030 in.) clearance between the impeller vanes and the housing.
To Replace
- The backplate is fitted with a DRY paper gasket to the cylinder block and retained by the single clamp screw ('7' of Fig.19).
BEFORE tightening, assemble front cover to the backplate, locating both the water pump insert in the cover and the oil seal on the crankshaft.
Move timing cover as an assembly including the backplate and its gasket, to ensure a maximum step between oil sump face on timing cover and cylinder block oil sump face and also between top faces of timing cover and backplate.
This step should not exceed .25 mm. (.010 in.).
- Remove timing cover, taking care NOT to move the backplate and its gasket and tighten clamp screw to the torque loading given in 'Technical Data'.
- Refit timing chain and crankshaft oil slinger.
- Apply jointing compound (Part No. A036 E 6027) to the cover joint faces and fit the cover.
It is important that the cover is correctly aligned and that the bolts are fitted to their correct locations (see Fig. 19).
Tighten the bolts to the specified torque loadings given in 'Technical Data'.
- Refit timing chain tensioner, sump, crankshaft pulley and water pump pulley and belt.
- Apply jointing compound (Part No. A036 E 6027) to a new gasket between timing cover and cylinder head. Replace cylinder head.
- Replace engine assembly.
E.31. - CRANKSHAFT SPROCKET - Section Menu
To Remove
- Remove the engine transmission assembly from the car (Section 'E.29') and mount on a suitable stand.
- Remove the front cover (Section 'E.30').
- Using a suitable extractor pull off the crankshaft sprocket.
To Replace
- Using a new key, press the sprocket on to the crankshaft ensuring that the slot is lined up with the key, and that the long boss is towards the main bearing journal.
- Refit the front cover.
- Refit the engine/transmission assembly into the car.
E.32. – CRANKSHAFT - Section Menu
To Remove
- Remove the engine/transmission assembly from the car (Section 'E.29').
Remove transmission from engine and mount engine on a suitable stand.
- Remove the camshafts cover (Section 'E.5').
- Set the valve timing marks in the timed position (Section 'E.8') then remove the crankshaft pulley (Section 'E.20').
- Remove the front cover (Section 'E.30'), crankshaft sprocket, (Section 'E. 31'), flywheel (Section 'E.25'), oil sump (Section 'E.16'), release the timing chain tensioner (Section 'E.6'), disconnect the timing chain (Section 'E.8'), and remove the rear oil seal carrier (Section 'E.26').
- Unscrew the connecting rod bearing cap bolts (the big-ends) two or three turns, and tap them to release the caps.
Completely remove the bolts and release the caps. Push the pistons up into the cylinder bores.
- Remove the main bearing cap bolts evenly and lift off each cap.
Lift out the crankshaft and remove the bearing liners and thrust washers.
- If the reground crankshaft is being fitted, it is important that the existing fillet radius between journals and webs MUST be maintained.
These measurements are:
Crankpin journals: .070/.084 in. (1.77/2.13 mm.)
Main bearing journals: .080/.094 in. (2.03/2.38 mm.)
Centre main bearing journal: see Fig. 20
To Replace
- Fit the clutch spigot bearing into the crankshaft (Section 'E.27').
- Using the new key, fit the crankshaft sprocket.
- Fit the new main bearing liners and replace crankshaft.
Fit new crankshaft thrust washers with the oil grooves towards the crankshaft flange.
Refit the main bearing caps (Section 'E.17').
This should be as given in 'Technical Data'.
- Using new bearing liners, refit the connecting rods to the crankshaft (Section 'E.18').
- Refit the rear oil seal carrier, reconnect the timing chain and re-adjust the tension, refit the oil slinger, flywheel, front cover, crankshaft pulley, and oil sump.
E.33. - JACKSHAFT (AUXILIARY SHAFT) - Section Menu
To Remove
- Remove the engine/transmission assembly from the car (Section 'E.29').
Remove transmission from the engine and mount on a suitable stand.
- Remove the cylinder head (Section 'E.l0") and front cover (Section 'E.30').
- Remove the jackshaft sprocket and the jackshaft thrust plate. Withdraw the jackshaft.
- If it is desired to renew the jackshaft bearing bushes, then the use of a Special Tool (Section 'E.37') for their removal and replacement is essential.
To Replace
- BEFORE fitting new brushes check that all oil ways in the cylinder block are clear.
Apply a sealing compound to the oil gallery plugs, prior to refitting.
- Using the Special Tools (Section 'E.37'), fit new jackshaft bushes, ensuring that the oil holes in bushes and cylinder block are aligned.
- The splits in the bushes should be upwards and outwards at 45° to the vertical.
- Fit a new dowel to the new jackshaft and slide the shaft into position. Using a new locking plate under the heads of the setscrews fit the thrust plate in its groove on the jackshaft. Tighten securing bolts to the torque loading given in 'Technical Data'. Check the shaft end-float (see 'Technical Data').
- Replace the jackshaft sprocket, the front cover and the cylinder head.
- Refit transmission to engine and replace engine/transmission assembly into car.
E.34. - CYLINDER BLOCK - Section Menu
To Remove
- Remove the engine/transmission from the car (Section 'E.29').
Remove transmission from engine and mount engine on a suitable stand.
- Completely strip all components from the engine following the procedures given in the previous chapters.
- Remove the oil pump filter gauze, oil pump inlet tube and oil return pipe.
- Remove the cylinder block from the stand.
To Replace
- Mount the new cylinder block on the stand.
- Fit the oil pump inlet tube and oil return pipe.
Press the pipe fully home to the full depth of the counter- bored hole.
Measured along the length of the pipe to the flange of the cylinder block this should read 16.5 cm. (6.5 in.).
Fit the filter gauze to the oil inlet tube.
- Rebuild the remainder of the engine by referring to the previous chapters.
- Rebuild the remainder of the engine and replace engine/transmission assembly into car.
E.35. - REBORING - Section Menu
When reboring the cylinder block to suit oversize pistons, each bore is machined to the actual diameter of the piston to be fitted, plus the specified clearance in the bore.
Maximum recommended oversize bore is PLUS (+) .380 mm. (.015 in.).
To Remove
- Remove the engine from car (Section 'E.29') mount on a suitable stand and completely strip off all components by following procedures given in previous chapters.
To Rebore
- Rebore cylinder block using proprietary boring equipment and adhering to the manufacturers instructions.
To Replace
- Rebuild engine and refit into the car by referring to the previous chapters.
E.36. - RUST INHIBITORS - Section Menu
E.37. - SPECIAL TOOLS - Section Menu
The foregoing sections have all been written without the mention of Special Tools, except in the case of the jackshaft bearing bushes, where the need for Special Tools is essential for their correct removal and replacement.
If much engine repair work is to be undertaken, it will be found more expedient to use some, if not all, the Special Tools from the following list.
These tools have been developed in conjunction with Ford Motor Company Limited and V.L. Churchill Limited from whom they are available.
Their address is:
V.L.Churchill & Co. Ltd.,
London Road, Daventry,
Northamptonshire, England.
Other Notes: [edit]
This area is a public scratchpad for notes.
Please be courteous with what you post, and do not erase someone else's work.
Section Menu
|